The Zeppelin Group’s declared goal is to completely avoid work-related accidents and occupational illnesses (Vision Zero). The following basic principles apply, and are anchored in the Group Policy on Occupational Health and Safety:
- The Management Board and managers have the primary responsibility and act as role models for safe and healthy working at Zeppelin. They take measures to maintain and continuously improve the health and performance of all employees in the long term. For this purpose, all the necessary means and resources (time, money, materials, and training) are made available to establish the occupational health and safety organization and the resulting measures.
- All employees are obliged to conduct themselves in such a way that they help prevent accidents, illnesses and hazards at work, both for themselves and for others. In doing so, they actively and consciously help to shape their daily actions. This means that the applicable occupational health and safety regulations are observed at all times, that the prescribed personal protective equipment (PPE) is always worn and that machines, devices and work equipment are only used for their intended purposes.
- All employees are encouraged to report or remedy faults and defects and to submit identified potential for improvement for a safe and healthy workplace. The aim is to achieve a continuous improvement in working conditions and a steady reduction in work accidents and occupational illnesses.
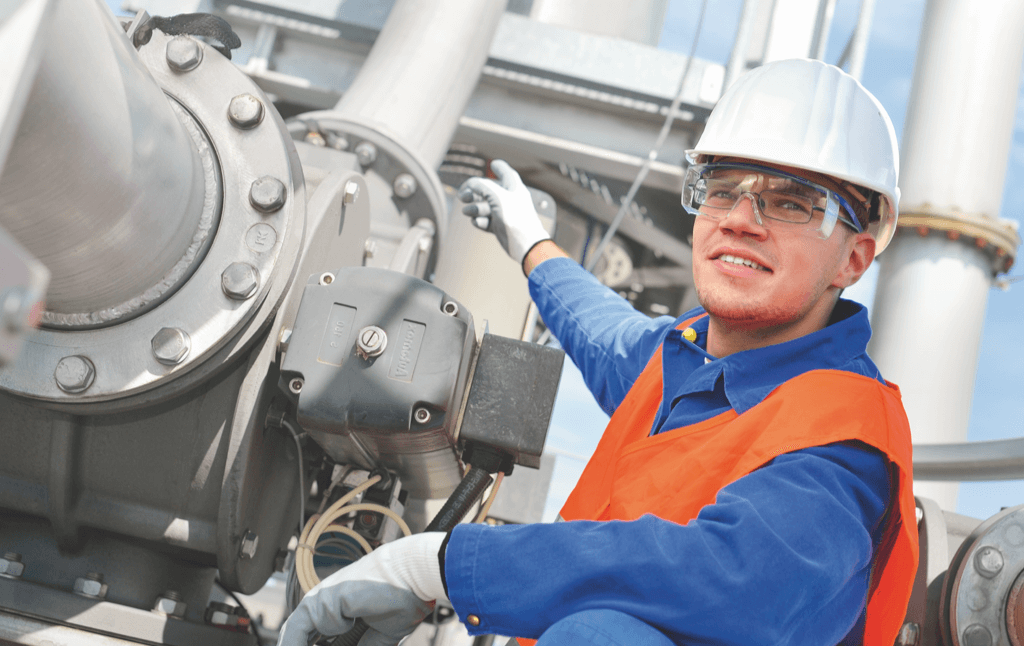
With the help of the occupational health and safety management system in accordance with ISO 45001, Zeppelin not only manages the alignment and achievement of its targets, but also monitors and documents the progress made. The scope of the certified occupational health and safety management system in accordance with ISO 45001 includes the companies Zeppelin GmbH, Zeppelin Rental GmbH, Zeppelin Baumaschinen GmbH, Zeppelin Power Systems GmbH, and Zeppelin Systems GmbH and their Group companies in Germany. ISO 45001 certification is only partially available abroad. To meet Zeppelin’s high standards abroad, the internal regulations are based on the existing occupational health and safety management system. The procedures and specifications for conduct in the event of accidents at work and their notification and reporting are regulated in procedural instructions. Development is recorded and monitored at every site of the German companies with more than 20 employees in quarterly meetings of the Occupational Health and Safety Committee. This is done with the participation of safety specialists and company physicians. A risk assessment is created for each activity in order to identify hazards in advance. Furthermore, inspections are carried out in all areas in order to identify risks and initiate measures. This process is documented in a procedural instruction. Regularly trained internal auditors reduce the risk of hazards through internal audits and site inspections. Site audits and certifications are carried out by third-party service providers. Due to the specifications of the supplier Caterpillar Inc. sources of hazards are presented using the contamination control process and stored alongside relevant measures.
To ensure the necessary knowledge and skills relating to health and safety at work, all employees take part in annual instruction. Responsibility for this lies with the respective managers. Good health and safety training can help prevent workplace accidents, protect employee health and increase productivity by minimizing potential risks. For this reason, Zeppelin offers two different occupational health and safety training courses across Germany, which also take job-specific topics into account. The safety of external companies and external personnel is just as important to Zeppelin as the safety of our own employees. For this reason, they are given instruction before they start work. Due to legal requirements in Germany, it is necessary to carry out a mandatory inspection for certain workplaces and the use of certain equipment and machines. Zeppelin complies with these requirements. In addition to this mandatory examination, Zeppelin also offers other voluntary occupational health services. These are specified individually at company level. Within Zeppelin GmbH, for example, sight tests and flu vaccinations are offered and have a high uptake among employees. Further campaigns are also planned for the coming years.
Progress in occupational health and safety
- Reducing work-related injuries by 10% per year by 2025
It is Zeppelin’s aim to provide all employees with a safe and healthy workplace, which is why Zeppelin has set itself the goal of reducing the work-related accident rate by 10% annually by 2025. The work-related accident rate, which includes the number of work accidents per 1,000 employees at Zeppelin, describes the frequency and severity of work accidents in combination with the number of days lost due to accidents.The definition of reportable work accidents at Zeppelin is as follows: “A reportable work-related accident is an accident that occurs due to or as a result of a person’s activity in the workplace, while working or while traveling on business, which requires medical treatment and leads to a period of absence lasting more than three calendar days after the day of the accident. Deaths are also accounted for and reported separately.”
The number of work-related accidents per 1,000 employees fell by about 8% last year. As a result, the defined target of a 10% reduction in 2022 was achieved. The majority of work-related accidents occurred in the Construction Equipment Central Europe SBU. In 2022, about 50% of the reported work-related accidents occurred there. In the Rental SBU, the Power Systems SBU, and the Plant Engineering SBU, the number of work-related accidents rose slightly compared with the previous year. This can be attributed, among other things, to the higher risks posed by working in the service or field service area. According to an analysis by the German companies, the majority of work-related injuries occur in the hand, followed by the ankle or foot and forearm. Zeppelin is continuing to work on reducing its occupational accidents. Among other things, an even more in-depth analysis of work-related accidents and corresponding instruction and awareness-raising of employees is planned for 2023.
Number of work-related accidents (> 3 days) per SBU | Unit | 2020 | 2021 | 2022 |
---|---|---|---|---|
Construction Equipment Central Europe SBU | Number | 114 | 126 | 114 |
Construction Equipment Eurasia SBU | Number | 3 | 7 | 7 |
Construction Equipment Nordics SBU | Number | 3 | 14 | 2 |
Rental SBU | Number | 65 | 59 | 64 |
Power Systems SBU | Number | 27 | 21 | 22 |
Plant Engineering SBU | Number | 17 | 16 | 22 |
Zeppelin Group1 | Number | 229 | 243 | 231 |
Work-related accidents per 1,000 employees2 | Number | 23.2 | 23.5 | 21.6 |
Fatal accidents at work | Number | 0 | 0 | 0 |
Lost Time Injury Frequency Rate3 | Rate | 12.3 | 12.5 | 11.5 |
1 Within Zeppelin GmbH, there have been no work-related accidents in recent years and therefore no days lost due to accidents. 2 The 1,000-person ratio is a general indicator of accident statistics in which the total number of reportable work-related accidents is determined for a defined period of time and converted to the number per 1,000 full-time employees (FTE). The period of consideration is a full calendar year. 3 LTIFR (Lost Time Injury Frequency Rate) was calculated with the occupational injuries > 3 calendar days and with the assumption of 230 working days and 8 working hours. Normalization factor: 1,000,000. |
- Reduce accident-related lost time (days) by 10% per year by 2025
The target of an annual reduction of 10% in days lost4 as a result of accidents was achieved in 2022 (2022: 12%) and is therefore at a similar level to 2020. It was also possible to reduce the number of days lost per 1,000 employees compared with the previous year. The Group will continue this trend on the path to “Vision Zero” with further targeted measures and work on a new understanding of safety.
Lost days per SBU | Unit | 2020 | 2021 | 2022 |
---|---|---|---|---|
Construction Equipment Central Europe SBU | Number | 2,933 | 3,554 | 3,042 |
Construction Equipment Eurasia SBU | Number | 87 | 505 | 480 |
Construction Equipment Nordics SBU | Number | 50 | 145 | 62 |
Rental SBU | Number | 1,321 | 1,174 | 1,208 |
Power Systems SBU | Number | 358 | 285 | 358 |
Plant Engineering SBU | Number | 456 | 549 | 311 |
Zeppelin Group5 | Number | 5,205 | 6,212 | 5,461 |
Lost days per 1,000 employees6 | Number | 527.3 | 600 | 510.4 |
5 The 1,000-person ratio is a general indicator of accident statistics in which the total number of reportable work-related accidents is determined for a defined period of time and converted to the number per 1,000 full-time employees (FTE). The period of consideration is a full calendar year. 6 The number of employees in recent years is shown in the Human Resources section. |
- Increasing the health rate to at least 97% by 2025 (status as of 2022: 95.5%)
Health promotion also played a particularly important role in 2022 due to the ongoing COVID-19 pandemic. Since the spring, there has been an increase in sick leave throughout Germany (source: Umbrella Association of Occupational Health Insurance Funds). The elimination of contact restrictions, the resumption of public life, and the relaxation of mask requirements played a major role in this regard. At Zeppelin, too, employees increasingly returned to the office, which increased the transmission of diseases. Overall, health management at Zeppelin is considered to be greatly important as it has a decisive influence on maintaining performance and on life satisfaction. Not only can it reduce absenteeism, but it can also lead to increased vitality and energy in everyday work. The health rate has been continuously between 95.5% and 96.5% over the past three years. The Construction Equipment Eurasia SBU and Zeppelin GmbH reported a particularly high health rate of almost 97%. The ongoing COVID-19 pandemic continues to have an impact on the way we work at Zeppelin. To support employees in this challenge, they also had the opportunity to participate in various campaigns and measures in 2022 via the Z FIT health initiative. The offering included a digital challenge on nutrition and sugar, weekly “moving breaks” to give employees the opportunity to integrate a little more movement into their everyday work, and a keynote speech on “How movement accompanies us through life”. To support our employees in balancing work and private life, famPLUS family service advisory services are also available in the areas of care advice, childcare, and psychosocial counseling.
Health rate as a percentage | 2020 | 2021 | 2022 |
---|---|---|---|
Construction Equipment Central Europe SBU | 95.6% | 95.6% | 95.4% |
Construction Equipment Nordics SBU | 96.2% | 96.5% | 95.6% |
Construction Equipment Eurasia SBU | 98.1% | 97.6% | 97.5% |
Rental SBU | 94.2% | 96.4% | 93.9% |
Power Systems SBU | 96.6% | 96.6% | 94.8% |
Plant Engineering SBU | 96.7% | 96.7% | 95.7% |
Zeppelin GmbH | 97.9% | 97.7% | 97.1% |
Zeppelin Group | 96.2% | 96.5% | 95.5% |
Occupational health and safety measures
Various technical measures were implemented at the sites to promote health and safety at work. To react more quickly in the event of an accident, Zeppelin Baumaschinen GmbH has installed new emergency telephones in the workshops, which establish direct contact with the emergency department. SOS alarm buttons were also introduced at SITECH Deutschland GmbH for lone workstations. In the wake of the COVID-19 pandemic, the flexible combination of office-based and mobile working has become well-established has proven very efficient in those areas of activity which allow it. In order to make spatial adaptations to meet the changing requirements of the new working environment (“new work”), an office concept with short-term workstations, open-space landscapes, desk sharing, project rooms and retreat areas for work requiring higher levels of concentration has already been implemented in several areas at the headquarters in Garching. In addition to the changes already mentioned, there are also height-adjustable tables at each of these workplaces to promote the health of employees. Besides the technical measures mentioned above, various company-specific organizational measures have been implemented. All managers of the Zeppelin Rental GmbH company were trained in the legal requirements in order to clarify the company’s obligations in the area of occupational health and safety. On the World Day for Safety and Health at Work, various types of campaigns were carried out within the company Zeppelin Systems GmbH. Interested employees were able to obtain information directly from the fire protection, rescue and health protection experts during fire protection exercises, fire extinguishing simulations, first aid workshops, visits to an ambulance and other information offers. In addition, an online presentation on the topic of “Psychological stress in the workplace” was offered.
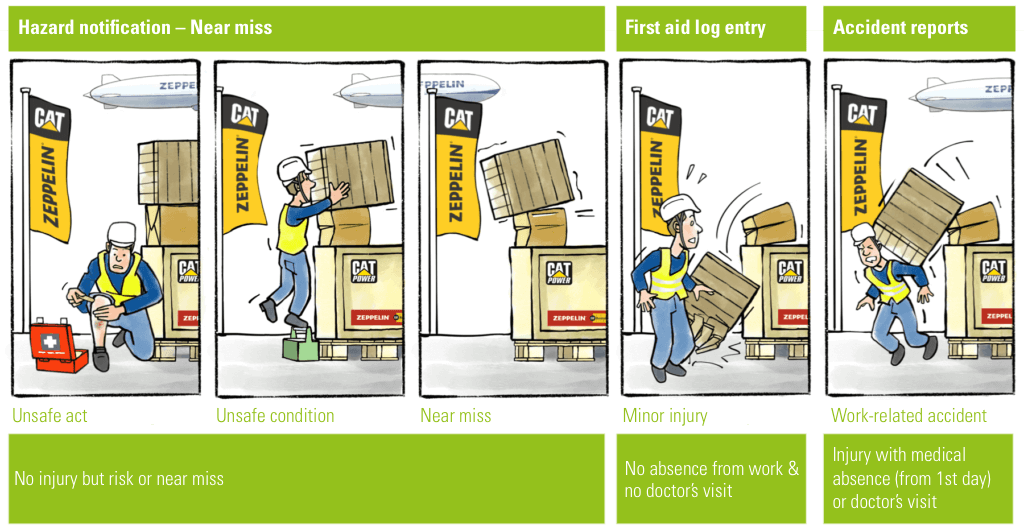
In 2022, a project was launched to digitally record accident log entries, near misses and work-related accidents throughout Germany as a first step. From 2023, an overview of the respective accidents in the “Accident Cockpit” should then be available for each site on a daily basis. The data is then aggregated automatically. In addition to the benchmark across different sites, analyses of accidents and potential hazards in everyday work can be recorded. The functions will then be gradually expanded in 2023.
4 The reduction is calculated in comparison with the previous year.